5G-enabled manufacturing: Ford deploys real-time process analysis and control
Critical automotive manufacturing processes, like robotic welding of components for electric cars, require detailed monitoring and quick configuration changes to optimize product quality. By analysing data in real-time from 5G-enabled sensors installed throughout the factory, auto manufacturer Ford Motor Co. is able to monitor and make rapid automatic adjustments to their production process.
This is one of the first use cases for the 5G Enabled Manufacturing (5GEM) project, a consortium of eight partner organizations (ATS Global, Ford, HSSMI, Lancaster University, TM Forum, TWI, Vacuum Furnace Engineering and Vodafone) exploring the use of 5G private networks in different manufacturing environments. The project is supported by the UK government’s 5G Testbeds and Trials Programme.
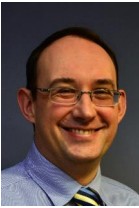
As Chris White, Manager of 5GEM at Ford, describes in this interview with Andy Tiller, 5G has great potential to revolutionise the production line.
AT: What problems are you trying to solve with the 5GEM project?
CW: Automotive plants are highly standardized. But repetitive processes that are assembling parts made to tight tolerances, can create variations that impact plant efficiency and product quality - subtle changes in temperature for example.
With 5GEM, we’re monitoring the manufacturing of vehicle electrical components through sensors attached to the machines, and processing machine data in real-time to determine if we need to quickly change settings to ensure quality.
AT: What kinds of sensors are you using and why?
CW: We have 5G-connected sensors monitoring laser welding for hairpin and battery-busbar joining. 5G delivers high throughput, enabling us to process large amounts of data quickly; for example, we check 192 welds per part at least 3 times per cycle. Once applied in a full-sized facility, we’ll be welding hundreds of connections per second. 5G’s low latency is also important because we need to be able to change the settings on the machines within milliseconds to continuously optimize production quality.
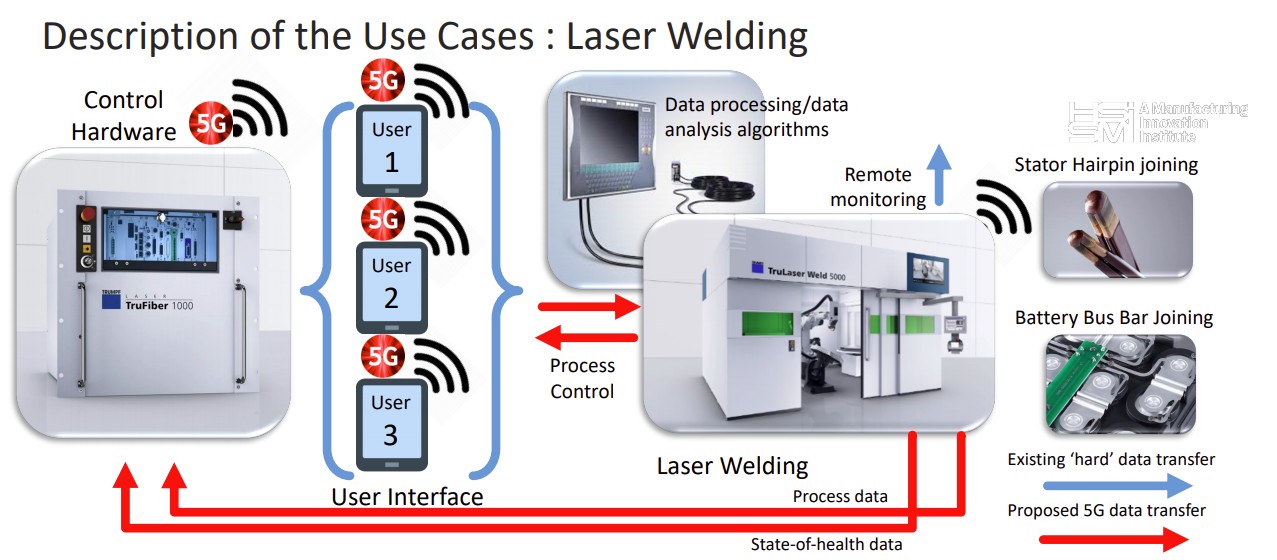
Laser welding machines retrofitted with 5G sensors and interfaces to monitor electric vehicle component manufacturing.
AT: What challenges have you faced so far with this project?
CW: Today’s equipment must be retrofitted; it doesn’t come into the factory with 5G-connected sensors pre-installed (although that’s the vision for the future). We need clear standards for equipment manufacturers to use, to ensure their equipment is ‘plug and play.’ TM Forum is leading the standards work within this project.
As ‘non-telecoms’ people, we at Ford had a limited appreciation of what is involved. It’s not yet an ‘out of the box’ solution, with assembly and testing also taking a significant amount of time.
AT: What other plans do you have for the 5GEM project?
CW: Intelligent maintenance is exciting - seeking to eliminate unnecessary downtime of the production line and enable secure remote support over the 5G network with our equipment suppliers using AR and VR.
We’re also keen to work across our mobile private network with the welding experts at TWI. We want to use 5G to create ‘digital twins’ of our processes so their experts can develop optimal welding solutions without stopping production.
There are many choices to make in how to adopt 5G. Hybrid or public networks will become more interesting when you start to interact with assets beyond the factory walls, such as logistics. When the product leaves the factory, its lifecycle continues. We’re using a dedicated mobile private network for maximum security, but with other configurations sensors in delivery vehicles will continue to keep track of journey conditions via the public 5G network.
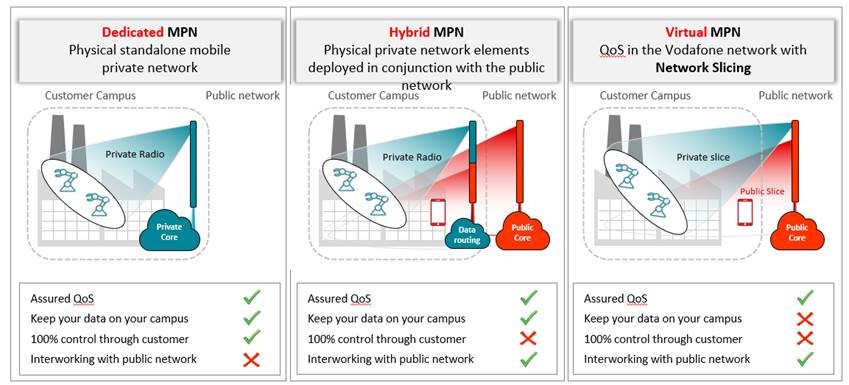
Mobile Private Network configuration options (Vodafone)
Thanks to Andy at TM Forum and Chris for this interview. Find out more about 5GEM on the UK5G website.
To read more from #DiversifyingTelecoms Campaign Week check out our landing page here.